Thanks to Paul Hanaphy and 3Dprintingindustry.com to write about our new resin. Full article can be found here. Netherlands-based 3D-printing resin manufacturer Liqcreate has added a new ultra-rigid ceramic-reinforced composite resin to its photopolymer resin portfolio. Called the Composite-X, Liqcreate’s latest photopolymer is designed to be the strongest and most rigid material in its engineering range. Featuring an impressive flexural modulus of over 9.0 GPa. After curing, the ceramic-reinforced resin can become even more rigid, showing its potential applications in the production of heavy-duty automotive or aerospace components.
Liqcreate’s growing photopolymer resin range
Liqcreate is specialized in 3D-printing resin development and manufacturing for MSLA, SLA and DLP 3D-printers. Clients utilize Liqcreate’s current resin portfolio within a range of applications, including the fabrication of prototype and end-use parts. Focussed in the medical, industrial, automotive, and consumer goods industries.
At present, the company’s resin range includes its premium, creative, engineering, castable, and general-purpose photopolymer resins, with each featuring different qualities to address a specific target market. Liqcreate’s general-purpose photopolymer resin, for example, provide users with a high level of print accuracy and a smooth finish. While its Hazard Glow resin yields parts with a unique glow-in-the-dark features.
Over the past months, Liqcreate expanded its resin portfolio, launching the dental-oriented Liqcreate Premium model resin in September 2019, followed by its Premium Flex and Tough resins for MSLA / LCD systems. Liqcreate also introduced the Tough-X and Flexible-X photopolymer resins last year. These resins feature strong impact-resistance and rebound properties, respectively.
Now, with the launch of its new Composite-X reinforced resin, Liqcreate has added an ultra-strong and stiff resin to its portfolio that’s completely different from the rest of its range. The polymer is reinforced by micro-nano ceramic composite particles, providing it with excellent strength characteristics. Once heated, it reacts by becoming significantly more rigid than conventional photopolymer resins.
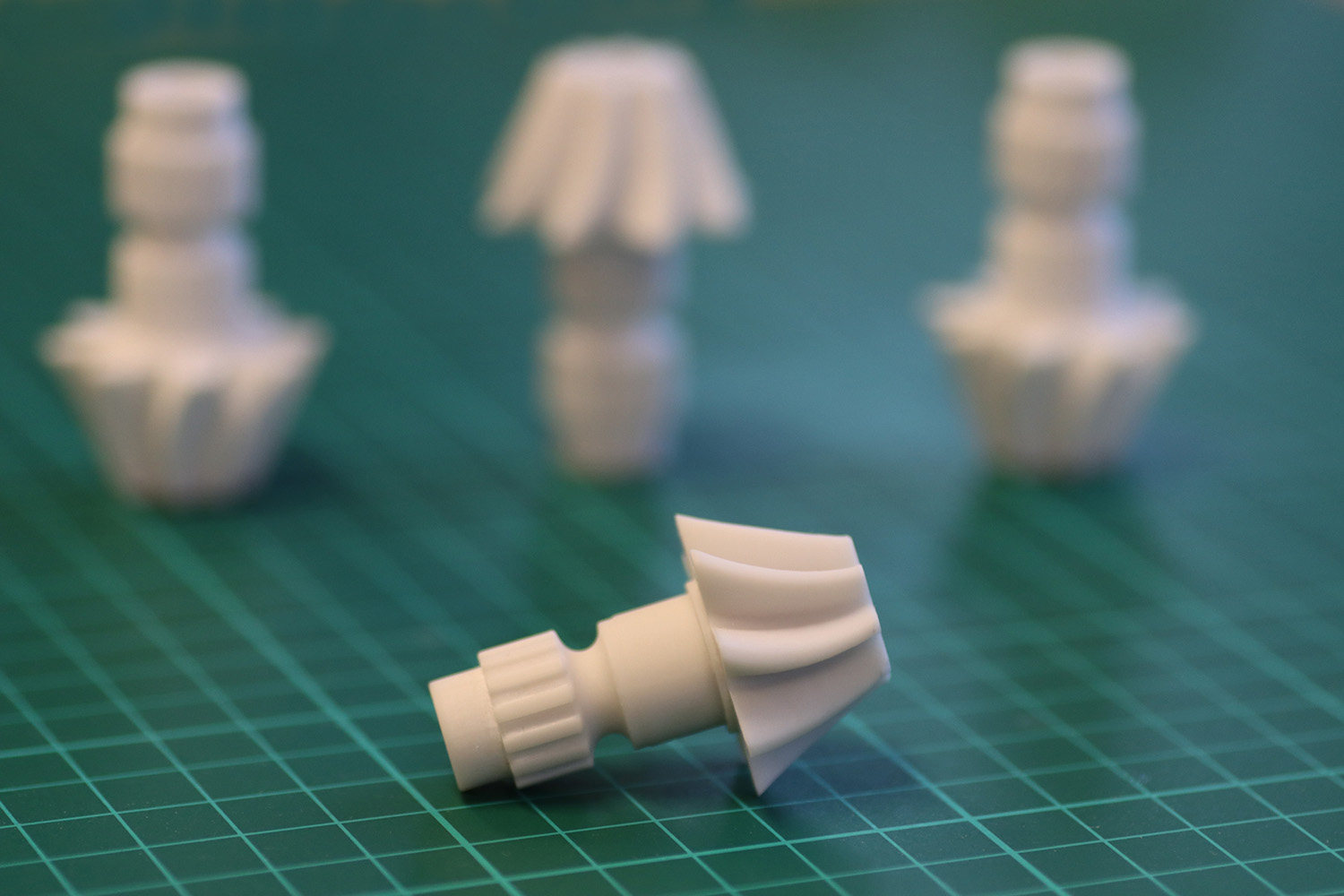
Liqcreate’s most rigid photopolymer yet!
Liqcreate’s reinforced Composite-X photopolymer resin has been designed with compatibility in mind. Focussed to work with most DLP, MSLA and laser-based reisn 3D-Printers operating with 385-420 nm wavelength light. The material itself is characterized by high chemical resistance and low shrinkage. Once UV-cured, the firm has shown that these properties can be dramatically enhanced.
During recent Liqcreate tests, Composite-X was 3D-printed into parts, then UV cured using a Wicked Engineering Curebox for 60 minutes. Before being thermally cured for another 2 hours. While the objects featured an initial flexural strength of 140-150 MPa. This rises to 150-170 MPa after heating treatment, representing a significant performance improvement.
Liqcreate’s post-cured parts also demonstrated other benefits. For instance an increased tensile and compression strength, as well as reduced water sorption. Compared to the firm’s other engineering resins, the Strong-X, the Composite-X was three times more rigid, potentially making it ideal for demanding aerodynamic applications like wind tunnel testing.
Designing the ideal resin for OEM partners
In addition to marketing its set resin range, Liqcreate also offers to develop customized resins for clients created for a specific application or to work with specific 3D-printing hardware. As part of the service, customers can request adjustments to a given resin property. This is for instance print speed, color, or mechanical properties, to ensure it prints perfectly on their chosen 3D-printing platform.
Effectively, the resin development process goes through a couple stages, beginning with the initial phases, in which engineers help clients create and evaluate their product plan. Once Liqcreate has started formulating the new 3D-printing resin, it then produces samples for customers to assess as well as system parameters, before the final resin is eventually shipped and manufactured.
Given that Liqcreate is an independent resin manufacturer with sales, R&D, and manufacturing facilities. It is also able to rapidly scale its production where needed. As a result, the company often targets large scale 3D-printing bureaus and manufacturers, with the aim of helping them quickly get their resin to market in quantities that won’t keep their clients waiting.
Recently, Liqcreate has also found that its service addresses dental clients’ needs, and its materials are often used to produce custom aligners. Consequently, although the firm has signed NDAs forbidding it from detailing new projects, it’s clear that its materials’ contact-friendly nature bodes well for the firm’s growth in the lucrative 3D-printing dental industry.