3D-printing flexible molds for reproducing wax silicone patterns and platinum cured silicone molds.
Silicones and rubbers are well known materials in the workshop of a moldmaker. With the introduction of flexible 3D-printing resins, more options are available to make custom flexible molds directly from a 3D-printer. Liqcreate partner Mr. Dombrun – known for his casting work –tested a range of flexible Liqcreate resins for this work.
In this article we are focusing on two workflows with flexible 3D-printed molds. The first one is to make a 3D-printed rubber mold for wax duplicates, for instance for crafting jewelry or artwork. In this case the flexible mold is 3D-printed and liquid wax is poured in the cavity. The wax is cooled and will solidify. After a few minutes it is hard enough to open the mold and a rigid piece of pure wax is produced. This part can be used for investment casting and turned to any metal.
In the second step the flexible molds are also 3D-printed with resin, although now the cavity is filled with RTV silicone (addition-cured, platinum catalyzed). The idea for this approach is that the true silicone part can be either used as a final part or as a mold master itself (for instance for pouring low melting point metals like tin and lead). In many cases the shape will be different then in our example. The workflow in this article shows that addition-cured, platinum catalyzed silicone can function with these 3D-printed photopolymer resins.

Image by Mr. Dombrun: Final casting of Ferris injection wax in a 3D-printed mold made with Liqcreate Flexible-X resin.
Testing flexible 3D-printing resin for reproducing wax patterns and platinum cured silicone.
At Liqcreate our three flexible resins were tested:
Premium Flex
Liqcreate Premium Flex is a translucent turquoise blue photopolymer resin with great processability and print speed on MSLA and DLP based 3D-printers. 3D-printed parts from this material have exceptional flexibility and a low surface hardness of 63 Shore A. It is suitable for prototyping uses.
Flexible-X is a firm and flexible material at the same time and very pleasant to handle... The details are well defined there too and after a passage in water the result is impeccable
Mr. Dombrun - Expert jewelry caster
Flexible-X
Liqcreate Flexible-X is an opaque black photopolymer resin for open MSLA, DLP and laser based 3D-printers. 3D-printed parts from this material have exceptional flexibility. Liqcreate Flexible-X is compatible with open DLP, LCD, MSLA and SLA 3D-printers in the range of 385 – 420nm. Its low hardness of 55 Shore A and elongation up to 160% makes it perfect for the manufacturing of soft touch and elastic parts for industrial use.
Elastomer-X
Liqcreate Elastomer-X is a clear photopolymer resin and can be processed on most resin based 3D-printers. 3D-printed parts from this material are exceptionally soft with a Shore A of 43 and has great flexibility. Its properties simulate soft TPU and silicone which makes it perfect for the production digital lattice foams, soft end of arm tooling (EOAT) for robots, grommets, bellows and elastic industrial parts.
Ferris injection wax
The Ferris injection wax was selected to use in this test. Ferris injection wax is a tough and hard wax that is ideal for molds with difficult corners. This waxes has a built-in release agents that are useful for easy extraction. It provides easy, clean extractions for intricate patterns. Injection Temperature: 155°F / 68°C.
Platinum cured RTV silicone with 3D-printing resin
The TFC Troll Factory Silicone Rubber Type 3 HB Tin Casting Heat Resistant RTV 1:1TFC was used as RTV silicone. This is an addition-curing (platinum catalyzed) 2-component silicone rubber that vulcanizes at room temperature (RTV). It is a pourable molding silicone which does not need external heat or vacuum. According to Mr. Dombrun this silicone is impeccable for an open mold and flows well into the cavities. It hardens in 90 minutes and there is no need to place it under vacuum. However, not possible to use in a closed mold.
Preparation of the flexible resin 3D-printed molds
Important to note that platinum catalyzed silicones are very sensitive to contaminations. Contaminations can come from the 3D-printing resin itself or from the surrounding. Next to potential problems with platinum catalyzed silicone curing, the contaminations can also interfere with the details in the mold. It is important to clean the molds well before working with platinum catalyzed silicone. After rinsing it with water, Mr. Dombrun uses a cleaning technique to get the flexible molds extremely clean. He uses two methods, first is with the Marabu 04060004873 window color kit. His advise is to make a homogeneous thick layer and let it sit for 2 hours. It will take the remaining dust out and can be used as protective film. Although it is important that the molds are as clean as possible before applying this layer. Alternatively he uses a pure latex. This is more liquid, dries faster and can be applied with a brush. If needed a second layer after 30 minutes. Products like Reschimica Latex Pro can be used, but it should be noted that most contain ammonia, which is not always wanted.
Simple and effective tip to remove dust or sanding residue and especially to protect and preserve printed pieces. After cleaning and drying completely, cover the surface with a windows color (used for synthetic stained glass).
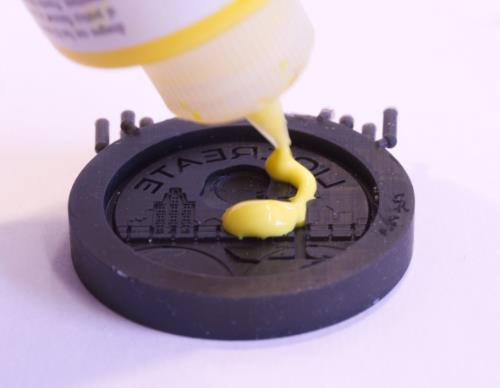
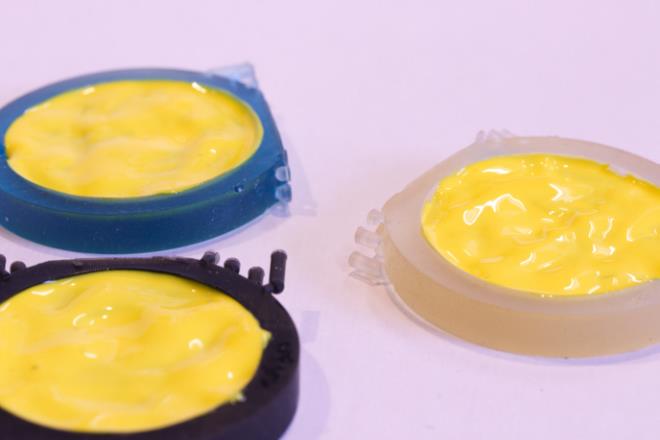
Simply spread in a thin layer and let dry well. The surface becomes translucent. Your piece is cleaned can be stored without problem.
You can simply remove the film, the surface of your piece is clean. Mr. Dombrun also uses this product for masking, for the conservation of printed jewels.
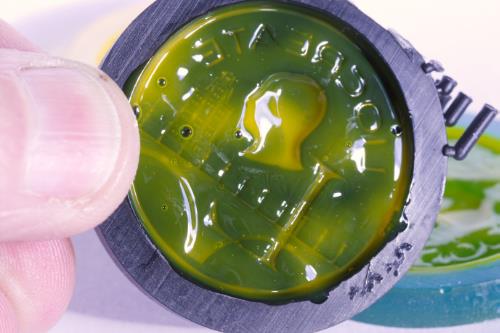
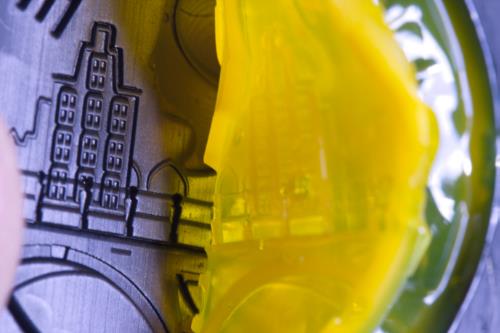
Testing 3D-printed rubber molds!
The flexible 3D-printed resin molds were 3D-printed on an Phrozen Sonic Mini 8K S resin 3D-printer with the default Liqcreate resin 3D-printing parameters. This first mold design was printed directly on the build plate with some additional supports on the sides.
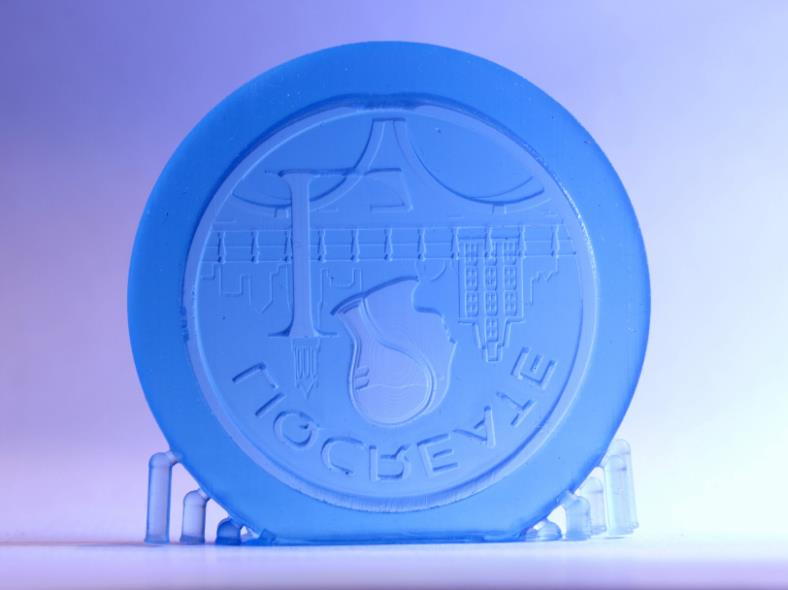
Image: Mold 3D-printed with Liqcreate Premium Flex prior to testing.
According to Mr. Dombrun “Premium Flex has a pleasant transparency, remains flexible without shape memory. The rubber is firm, see the behavior with wax at 78-83°C.”
In the default print settings and this orientation some light bleeding is present in this translucent material. Some small cavities in the background and the letters were not printed in full detail. The parameters and orientation can be improved to reduce these defects.
Image: Flexible resin 3D-printed mold made with Liqcreate Premium Flex after injecting with ferris injection wax.
The wax casting was done at roughly 80°C. Quite some details are missing, not the ideal combination of material – process – wax. Likely the casting and/or mold temperature should be higher.
Image: Mold 3D-printed with Liqcreate Premium Flex after pouring RTV silicone (platinum catalyzed) in the mold cavity.
The RTV silicone (addition-cure, platinum catalized) on the other hand performed much better and the details are visible. Almost a complete 1-on-1 copy of the flexible 3D-printed resin mold in silicone. According to Mr. Dombrun ”No problem with pouring the platinum catalyzed RTV silicone in an open mold, without vacuum and no reaction with the flexible 3D-printing resin. See if it goes well with a closed mold! In any case, very good details.”
Same test was performed with Liqcreate Elastomer-X. The mold was positioned in the same way on the same printer. Although some details are better compared to Premium Flex, some parts like the letter “L” could be more detailed on the base. More optimal orientation and slightly lower exposure time can help. This is not tested in this experiment.
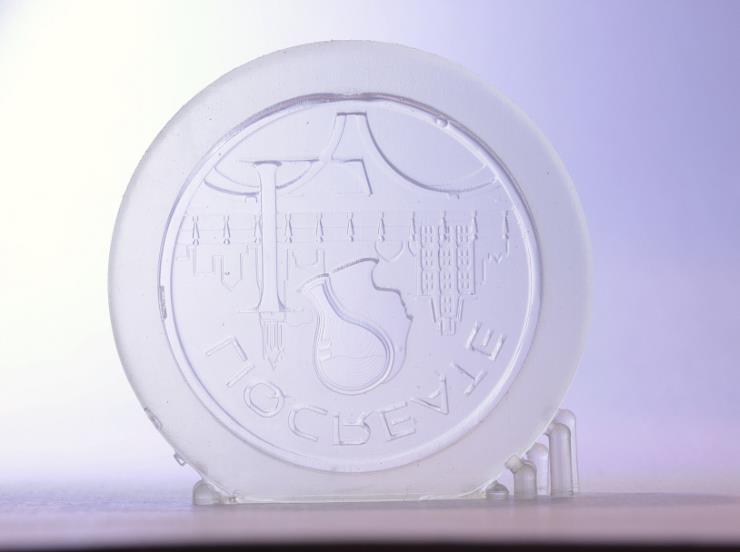
Image: Mold 3D-printed with Liqcreate Elastomer-X prior to testing.
Similar results with the injection of wax (poor result) and with the pouring of RTV silicone (good result) were obtained compared to Premium Flex. According to Mr. Dombrun “However, more practical for wax injection, I made three tests with different temperatures and pressure, no fine details. And the mold surface a little sticky from the start.“
Image: Mold 3D-printed with Liqcreate Elastomer-X after injecting with ferris injection wax.
Image: Mold 3D-printed with Liqcreate Elastomer-X after pouring RTV silicone (platinum catalyzed) in the mold cavity.
The RTV silicone copied almost all details of the Elastomer-X mold and worked well.
Same test was performed with Liqcreate Flexible-X. The mold was positioned in the same way on the same printer. As this material is opaque black, light bleeding is less of an issue here and the details are nicely printed in this mold with the default 3D-printing parameters.
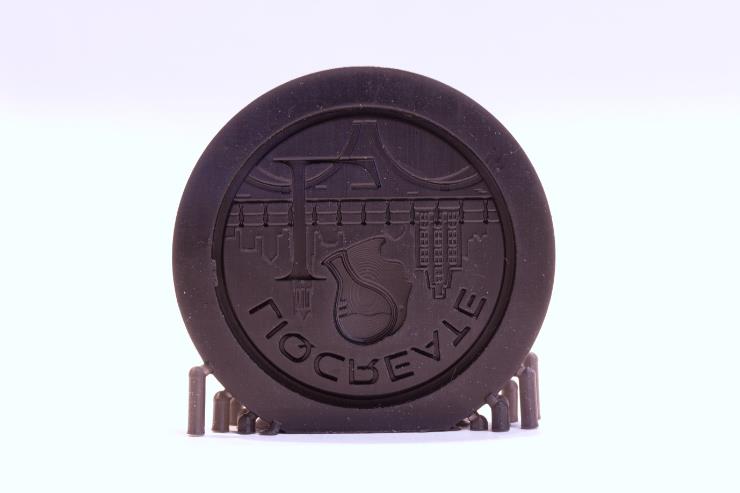
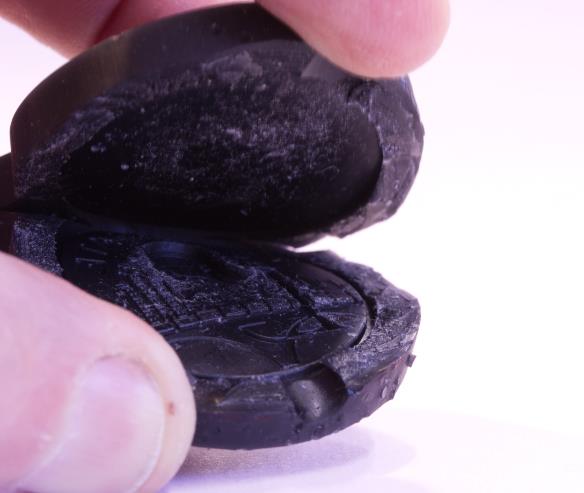
Image: Molds 3D-printed with Liqcreate Flexible-X prior to testing.
According to Mr. Dombrun “Flexible-X, a firm and flexible material at the same time and very pleasant to handle. Many details and luckily, I received a usable closed mold. So I cut the closed mold in two, the details are well defined there too, it gets dusty quite quickly, but after a passage in water the result is impeccable.”
Image: Mold 3D-printed with Liqcreate Flexible-X after injecting with ferris injection wax.
Both the closed and open mold gave good results. In some corners a little text is missing as a higher wax temperature / warmer mold was needed. According to Mr. Dombrun: “Single or double mold, the result is sufficient to move on to casting. Ideally you make a two-part mold with an edge of 8 to 10 mm as well as a conical orifice for injection. For me, this resin is well suited for this type of molding”
Image: Mold 3D-printed with Liqcreate Flexible-X after pouring RTV silicone (platinum catalyzed) in the mold cavity.
As expected the RTV rubber also performed well with Flexible-X molds.
Image: Comositions of Liqcreate flexible resins 3D-printed as mold for pouring RTV silicone (platinum catalyzed) in the mold cavity.
Summary of first wax and silicone trial
To quote Mr. Dombrun: “If you want to print a single or double mold to inject wax into for casting molten metal, or in a single mold for silicone (for soap, candle or other molding), the Flexible-X is the best choice: Flexible. It is strong, no shape memory, very good surface finish, resists hot wax well and offers superb details with silicone. After testing, here is the design of the ideal mold for injection wax”
Perfectioning the process.
With the first open mold design, it is difficult to control the back side of the part. The first open mold was printed only successful in Flexible-X resin. Mainly because the design missed drain holes. After designing a new 2 part mold, testing continues with Flexible-X.
The molds had sharp angles and therefor it was printed in an angle on supports in the printer. Due to the orientation there are layer lines in the mold and also in the wax pieces that came out of this mold. The test was not extended due to time constraints but if the mold was designed in a way that it could be printed at a 90° angle, the quality would be even better!
The details are very well visible. Additionally the mold did not show any sign of degradation after 20 shots. This Ferris injection wax has no adhesion to the Flexible-X molds so it is expected to survive for a while.
Flexible-X
Liqcreate Flexible-X is an opaque black photopolymer resin for open MSLA, DLP and laser based 3D-printers. 3D-printed parts from this material have exceptional flexibility and great rebound properties. Liqcreate Flexible-X is compatible with open DLP, LCD, MSLA and SLA 3D-printers in the range of 385 – 420nm. Its low hardness of 55 Shore A and elongation up to 160% makes it perfect for the manufacturing of soft touch and elastic parts for industrial use. Compatible with (RTV) platinum catalyzed, addition-cured silcones.
Key benefits |
3D-Printer compatibility |
· High Elongation | · Epax3D Series & Nexa3D XiP |
· Excellent Rebound | · Phrozen & Anycubic series |
· Good Tear Strength | · Shining3D AccuFAB-L4K |
· Durable Soft Touch | · Asiga & W2P series |
· Compatible with (RTV) platinum catalyzed, addition-cured silcones | · And many more |